The Ultimate Guide to Soldering Plumbing: Step-by-Step Tutorial for Leak-Free Joints
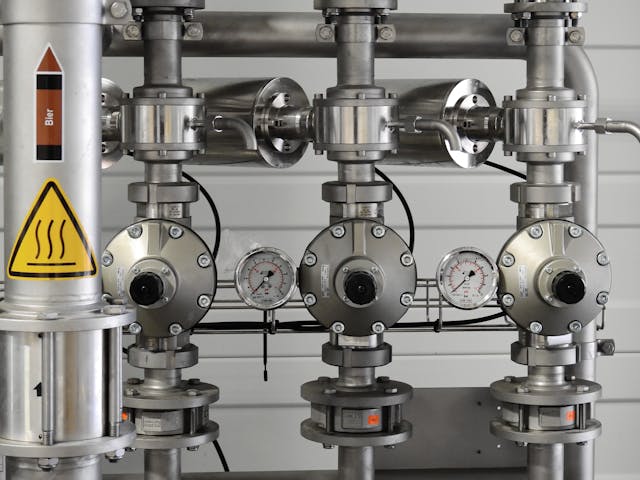
Key Takeaways:
- Proper Preparation is Crucial: Clean and prep both the pipes and fittings thoroughly before soldering. This ensures a strong bond and prevents leaks.
- Master the Technique: Control the heat and solder flow. Apply heat evenly and use just enough solder to create a tight, leak-proof seal.
- Safety First: Always use proper safety gear, including gloves and safety glasses, to avoid burns and injuries. Working in a well-ventilated area is also essential.
Soldering copper pipes is a crucial skill for any DIY plumber or homeowner. It’s the most reliable way to create strong, leak-free connections between pipes. When done properly, soldered joints can last for decades without issues.
This article will walk you through the step-by-step process of soldering copper pipes like a pro. We’ll cover everything from choosing the right tools and materials to cleaning and prepping the pipes, applying flux and solder, and testing for leaks.
Gather Materials and Tools
Before soldering copper pipes, it’s crucial to gather all the necessary materials and tools. Having everything ready will make the process smoother and more efficient.
Copper Pipe and Fittings
You will need copper pipes and fittings that match the size of the project. It’s important to use high-quality, clean copper components to ensure a strong, leak-free connection. Opt for Type L or Type M copper pipes, as they’re commonly used in residential plumbing and are available in various diameters.
Propane or MAPP Gas Torch
A reliable heat source is essential for soldering. We recommend using a propane or MAPP gas torch, as they provide the necessary heat to melt the solder and create a secure bond. MAPP gas burns hotter than propane, allowing for faster soldering, but either will work well for most plumbing projects.
Soldering Flux and Lead-Free Solder
Soldering flux is a paste or liquid that helps the solder flow evenly and adhere to the copper surfaces. Always use a lead-free, water-soluble flux to ensure the safety of drinking water. For the solder, choose a lead-free variety with a tin-antimony or tin-silver composition, as required by plumbing codes.
Pipe Cutter, Emery Cloth, Wire Brush
To prepare the copper pipes for soldering, you will need a few essential tools:
- A pipe cutter to make clean, straight cuts on the copper pipes
- Emery cloth or fine-grit sandpaper to clean and roughen the surfaces of the pipes and fittings
- A wire brush to remove any debris or oxidation from the inside of the fittings
Having these tools on hand will help create clean, well-prepared surfaces for a successful soldering job. Also, visit our plumbing page
Prepare the Pipe and Fittings
Properly preparing the copper pipes and fittings is crucial for achieving a successful soldered joint. Here’s how to ensure the surfaces are clean and ready for soldering.
Measure and Cut the Copper Pipe
Start by measuring the copper pipe to the desired length, then use a pipe cutter to make a clean, square cut. A hacksaw or demo saw also works, but a pipe cutter ensures a neater cut. Next, rotate the cutter around the pipe, tightening it slightly with each rotation until it cuts through.
Remove Burrs and Clean the Pipe
After cutting, remove the burrs and oxidized finish from both the inside and outside of the pipe. Use a reaming tool or 120-grit sandpaper to clean the exterior and a pliers or square-edged tool to remove interior lips that could impede water flow. Larger tubing cutters often have built-in deburring tools for convenience.
Clean and Prepare the Fittings
Next, clean the inside of the copper fitting hubs using an Oatey fitting brush or emery cloth rolled into a small cylinder. Cleaning the joining surfaces of both the pipe and fittings is essential, even if they appear shiny and new. This ensures a secure, leak-proof joint when soldering.
Apply Soldering Flux
Applying flux is a crucial step in the soldering process. It ensures that the solder properly adheres to the copper, creating a strong, leak-free joint.
Importance of Flux in Soldering
Flux plays a vital role in soldering by removing oxides and other impurities from the copper surfaces, allowing the solder to flow smoothly and evenly. It also helps to prevent oxidation during the heating process, ensuring a clean and secure bond between the pipe and fitting.
Without flux, the solder won’t be able to penetrate the joint properly, resulting in a weak connection that’s prone to leaks. Flux acts as a catalyst, promoting the flow of molten solder into the gaps between the pipe and fitting, creating a seamless and durable seal.
Applying Flux to Pipe and Fittings
To apply flux, use an acid brush or a small paintbrush. First, dip the brush into the flux and apply a thin, even layer to both the inside of the fitting hub and the outside of the pipe end. It’s important to cover the entire surface that will be in contact with the solder.
Be careful not to apply too much flux, as excess can cause the solder to flow beyond the joint or create unsightly residue. A light coating is sufficient to promote proper solder adhesion. After applying the flux, immediately insert the pipe into the fitting, giving it a slight twist to ensure even distribution of the flux.
If you are soldering multiple joints, apply flux to each joint individually, just before soldering, to prevent the flux from drying out or becoming contaminated. This ensures that each joint receives the full benefit of the flux and results in a consistent, high-quality soldered connection. We also offer residential and commercial electrical services in Knoxville.
Assemble the Joint
Now that the copper pipes and fittings are clean and fluxed, it’s time to assemble the joint. Let’s walk you through the process of inserting the pipe into the fitting and ensuring proper alignment for a strong, leak-free connection.
Insert Pipe into Fitting
Start by carefully inserting the cleaned and fluxed pipe into the fitting hub. It’s essential to push the pipe firmly into the fitting until it reaches the stop or shoulder inside the hub. This ensures that the pipe is fully seated and creates a strong connection when soldered.
If you encounter resistance while inserting the pipe, double-check that both the pipe and fitting are clean and free of debris. A slight twisting motion can help the pipe slide into the fitting more easily. However, avoid forcing the pipe, as this may damage the fitting or cause misalignment.
Ensure Proper Alignment
Once the pipe is inserted, visually inspect the joint to ensure that the pipe and fitting are properly aligned. Proper alignment is crucial for creating a strong, leak-free joint and maintaining smooth water flow through the plumbing system.
Check that the pipe is straight and not tilted or angled within the fitting hub. If necessary, make slight adjustments to the pipe’s position while it’s still movable. For joints that require a specific orientation, such as 90-degree elbows or tees, pay extra attention to ensure the fitting is oriented correctly before soldering.
If you are working with multiple joints in a confined space, dry-fit the entire assembly before soldering to ensure proper alignment and fit. This allows me to make any necessary adjustments before applying heat and solder, saving time and materials in the long run. Have air gaps in plumbing? Read our guide on plumbing air gaps to figure out the issue.
Heat and Solder the Joint
Once the copper pipes and fittings are cleaned, fluxed, and properly assembled, it’s time to heat the joint and apply the solder. Here’s how to do it, step by step:
Heating Technique Using the Torch
Use a MAPP torch and adjust the flame so the blue cone in the center is about 1/4″ long. The longer the cone, the hotter the flame. Hold the flame so the tip (the hottest point) just touches the fitting. It’s not necessary to heat the copper tube directly because the fitting quickly conducts the heat to the tube inside the joint.
Next, heat the joint with a torch, moving the cone of the flame back and forth for even heating. As you heat the joint every few seconds, remove the heat and touch the tip of the solder to the joint to see if the metal is hot enough to melt the solder. If it does not melt or only slightly melts, remove the solder and continue to heat until the solder easily melts onto the copper.
Applying the Solder
Once the solder easily melts onto the joint, apply enough solder to fill the joint and then reheat the fitting, which draws the solder into the joint. Also, hold the solder opposite the flame (the coolest point) to make sure all parts of the joint are hot enough. Solder won’t fill spots cooler than its melting point.
Continue this until the solder melts and flows into the joint. The joint should appear full on all sides. I’ll know I’ve applied enough solder when there is a silver band the entire way around the joint. When this band is flush with the surface of the pipe, I’ll know that solder has been drawn into the joint.
If you apply too much solder, a small solder bubble will form on the lower side of the joint. This doesn’t affect the integrity of the joint but can look a bit messy. Also, excess solder can flow into the inside of the pipe, which can interfere with flow if the quantity is large. Also, read our guide on galvanized plumbing.
Allowing the Joint to Cool
After applying the solder, give the joint 30 to 45 seconds to cool and harden before putting any pressure on it. It’s important to be careful as the joint will still be too hot to touch during this time.
It is also really helpful to have someone else assist with the soldering process. One person can use the torch while the other applies the solder. That way, you can start soldering right when the torch is off the pipe. The best way is in fact to go for a professional plumber.
Inspect and Test the Soldered Joint
After you have soldered the joint, it’s crucial to inspect the work and test the plumbing system to ensure a strong, leak-free connection.
Visual Inspection for Leaks or Imperfections
Once the soldered joint has cooled completely, I carefully examine it for any signs of leaks or imperfections. I look for:
- A smooth, even band of solder around the entire joint, flush with the pipe surface
- No gaps, pinholes, or rough spots in the solder
- No discoloration or charring of the copper, which could indicate overheating
- No excess solder drips or bulges that could restrict water flow
Pressure Testing the Plumbing System
To confirm the integrity of soldered joints and the entire plumbing system, conduct a pressure test:
- I ensure all soldered joints are cool and fully set.
- I cap or plug all openings in the plumbing system, such as faucets, valves, and drains.
- Using a pressure gauge and a hand pump or compressor, I pressurize the system to about 1.5 times the normal operating pressure (typically 150 psi for residential plumbing).
- I monitor the pressure gauge for at least 15 minutes to check for any drops in pressure, which could indicate a leak.
- If the pressure remains steady, I visually inspect each joint for leaks, dampness, or drips.
- If I detect a leak, I mark the location, depressurize the system, drain the water, and resolder the faulty joint.
- Once all leaks are repaired, I repeat the pressure test to confirm the system is leak-free.
By thoroughly inspecting and testing soldered joints, ensure a reliable, durable plumbing system that will provide years of trouble-free service.
Tips for Soldering in Tight Spaces
When soldering plumbing in tight spaces, like under sinks or in cramped utility rooms, there are a few tricks you can go for:
Use a Compact Torch
A compact torch, like a micro torch or a pencil flame torch, is essential for soldering in tight spaces. These torches provide a precise, focused flame that’s easier to control in confined areas. A butane micro torch with a fine tip works best for me, as it heats the joint quickly without risking damage to nearby surfaces.
Protect Surrounding Surfaces
Before soldering, always take a moment to protect any surfaces near the joint that could be damaged by the torch’s heat. Use a heat shield, like a piece of sheet metal or a heat-resistant mat, to deflect the flame and prevent scorching or melting. For extra protection, you can sometimes wrap nearby pipes or wires with a heat-resistant tape.
Pre-Assemble the Joint
In tight spaces, it is helpful to pre-assemble the joint before soldering. I dry-fit the pipes and fittings, making sure everything aligns correctly and fits snugly. If needed, make any adjustments to the pipe length or fitting orientation. Once satisfied with the fit, disassemble the joint, clean and flux the surfaces, and reassemble it for soldering.
Use a Soldering Aid
A soldering aid, like a third hand tool or a pipe support, can be a lifesaver when working in tight spaces. These tools hold the pipes and fittings securely in place, freeing up your hands for soldering. Position the soldering aid to support the joint at the correct angle, ensuring proper alignment and a smooth solder flow.
Work in Stages
When dealing with multiple joints in a confined space, work in stages to avoid overheating the area. Solder one joint at a time, starting with the most difficult or least accessible one. After completing each joint, give the area a few minutes to cool down before moving on to the next one. This approach prevents the heat from building up and potentially damaging nearby joints or surfaces.
Clean as You Go
Soldering in tight spaces can get messy, with flux residue and solder drips accumulating quickly. To keep the work area clean and prevent contamination of future joints, clean as you go. Keep a damp rag or sponge nearby to wipe away any excess flux or solder immediately after completing each joint. This habit not only maintains a tidy workspace but also helps me spot any imperfections or leaks right away.
By following these tips, you will be able tackle soldering jobs in even the tightest spaces with confidence and achieve professional-looking results. Remember, patience and attention to detail are key when working in confined areas. Take your time, focus on one joint at a time, and don’t be afraid to pause and reassess if something doesn’t feel right. With practice and persistence, you’ll be soldering like a pro in no time, no matter how challenging the space may be.
Conclusion
Soldering copper pipes may seem daunting at first, but with the right tools, materials, and techniques, it’s a skill that anyone can master. By following the step-by-step guide, you’ll be able to create strong, leak-free connections that will stand the test of time.
Remember to take your time, practice patience, and pay attention to the details. Clean and flux your pipes properly, heat the joint evenly, and apply the solder smoothly for the best results. Don’t forget to inspect and test your work to ensure a reliable, long-lasting plumbing system.
With these tips and techniques, you’ll be soldering like a pro in no time. Embrace the challenge, and take pride in your newfound skills as you tackle your next plumbing project with confidence.
FAQs
What are the basics of soldering copper pipe?
The basics of soldering copper pipe involve understanding how to prepare the copper joints, applying flux, heating the fitting with a propane torch, and melting solder into the joint to create a strong bond. Proper technique is essential for achieving a leak-free connection.
How do I solder vertical copper pipe?
To solder vertical copper pipe, you need to ensure that you have proper support for the pipe and fittings. Heat the fitting evenly with a propane torch and then touch the solder to the joint. The heat will draw the solder into the joint, ensuring a tight seal.
What tools do I need to learn how to solder copper?
To learn how to solder copper, you will need a propane torch, solder (preferably lead-free), flux, a pipe cutter for cutting copper, and a wet rag for cooling joints if needed. Additionally, having a soldering iron handy can be useful for smaller jobs.
How do I prepare the inside of the pipe before soldering?
Before soldering, clean the inside of the pipe and the outside of the fitting with sandpaper or a wire brush to remove any oxidation. Then, apply a layer of flux on both surfaces to help the solder flow properly into the joint.
How much solder should I use when soldering copper pipes?
The amount of solder to use should be enough to create a small bead around the joint, typically about an inch of solder for each copper joint. Make sure the solder fills the gap thoroughly but avoid excessive solder that could cause drips.
Can I use lead solder for copper plumbing?
It is not recommended to use lead solder for copper plumbing as it can pose health risks. Instead, opt for lead-free solder, which is safer and compliant with plumbing codes.
What is the role of flux in soldering copper pipes?
Flux plays a crucial role in soldering copper pipes by preventing oxidation during the heating process. It allows the solder to flow more easily into the joint and ensures a stronger bond by cleaning the surfaces as you heat the fitting.
What are some common mistakes to avoid when soldering copper?
Common mistakes include not cleaning the surfaces properly, using too much or too little solder, overheating the joint, and failing to apply flux. Each of these can lead to weak connections or leaks in your copper plumbing.
How do I ensure a leak-free joint when soldering?
To ensure a leak-free joint when soldering, make sure to clean the surfaces thoroughly, apply the right amount of flux, heat the fitting evenly, and touch the solder around the joint to let it flow into the gap. A proper technique will help you create a durable and watertight seal.